1. 引言
机器视觉定位与引导系统是现代自动化生产中的核心技术之一。随着工业4.0和智能制造的不断推进,机器视觉已经成为重要的自动化工具之一,用于实现精准的定位和引导功能。该系统通常结合相机、图像处理算法和控制设备,实现精确的物体识别、定位、导航与引导功能。
本方案将介绍机器视觉定位与引导系统的设计,包括优选的元器件、器件的作用、功能以及如何在系统中应用。通过详细的电路框图和元器件的选择依据,帮助设计人员实现高效、稳定的系统。
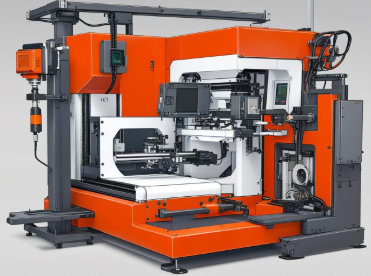
2. 系统架构设计
机器视觉定位与引导系统通常由以下几个关键模块组成:
图像采集模块:采用工业相机获取现场图像。
图像处理模块:对采集到的图像进行分析和处理,获取目标的位置信息。
控制模块:根据图像处理结果控制定位与引导设备,通常为PLC或嵌入式系统。
执行模块:通过驱动设备进行实际的定位或引导操作,通常为伺服电机、步进电机等。
3. 主要元器件选择
在机器视觉定位与引导系统中,以下元器件至关重要。每个元器件都具有特定的功能,合理的选择这些元器件能有效提升系统性能。
3.1 工业相机
3.2 图像处理单元(GPU)
优选型号:NVIDIA Jetson Xavier NX
作用:用于处理采集到的图像数据,通过深度学习、计算机视觉算法等方法分析物体位置、方向等信息。
为什么选择这颗元器件:NVIDIA Jetson Xavier NX是一款集成了强大计算能力的嵌入式AI平台,拥有高效的GPU加速,能够处理复杂的图像处理算法和深度学习模型,具有高性能、低功耗的特点。它非常适合用于实时图像处理、机器视觉和定位系统中。
3.3 电机控制模块
优选型号:STMicroelectronics L6234
作用:负责控制步进电机或伺服电机的精确运动,实现物体的定位与引导。
为什么选择这颗元器件:L6234是一款三相驱动器,具有较高的输出功率和稳定的电流控制功能。它支持PWM调制和过载保护,适用于步进电机和伺服电机的精确控制,能够精确调节电机的运动,以确保定位与引导的精度。
3.4 传感器
优选型号:Keyence LV-N Series Laser Displacement Sensor
作用:用于提供物体的实时距离信息,辅助定位精度的提高。
为什么选择这颗元器件:Keyence的激光位移传感器具有极高的测量精度,能够以纳米级别的精度进行距离测量,适用于精密的机器视觉定位系统。其高灵敏度和高速响应可以确保在复杂环境下仍然能准确获取位置信息。
3.5 控制单元
优选型号:Beckhoff CX5130嵌入式控制器
作用:负责控制整个系统的运作,包括图像采集、数据处理以及执行模块的控制。
为什么选择这颗元器件:Beckhoff CX5130具有强大的控制能力,支持多种通讯协议,并且能够同时处理多个任务。在工业环境中,它的高稳定性和实时性使其成为控制单元的优选。
3.6 电源管理模块
优选型号:Texas Instruments TPS5430
作用:为系统中的各个模块提供稳定的电源,确保系统的可靠运行。
为什么选择这颗元器件:TPS5430是一款高效的同步降压转换器,具有较高的效率和良好的负载响应能力,能够为机器视觉系统提供稳定的电压,减少电源噪声对图像采集与处理的干扰。
4. 系统功能与应用
机器视觉定位与引导系统在工业自动化中的应用广泛。其主要功能包括:
精确定位:通过图像处理和传感器反馈,系统可以实现高精度的定位。
路径引导:根据系统的定位信息,执行引导任务,使物体按照预定路径移动。
缺陷检测与质量控制:机器视觉系统能够检测物体的尺寸、形状、颜色等信息,确保产品质量。
5. 电路框图
以下是机器视觉定位与引导系统的电路框图:
+---------------------+
| 工业相机 (Basler) |
+---------------------+
|
v
+---------------------+
| 图像处理单元 (Jetson) |
+---------------------+
|
v
+---------------------+
| 电机控制模块 (L6234) |
+---------------------+
|
v
+---------------------+
| 执行模块 (步进电机) |
+---------------------+
6. 机器视觉算法的选择与优化
在机器视觉定位与引导系统中,算法的选择对整体性能至关重要。不同的应用场景需要不同的视觉处理方法,以提高识别精度和响应速度。
6.1 目标检测与识别
目标检测是机器视觉定位系统的核心环节,通常采用以下几种方法:
传统图像处理方法(边缘检测、形态学处理):适用于规则形状目标的识别,例如工业零件的定位。
基于特征点匹配的方法(SIFT、ORB):适用于复杂背景中的目标识别,如PCB板上的元件定位。
深度学习方法(YOLO、Faster R-CNN):适用于复杂环境下的实时目标检测,例如自动驾驶和物流分拣。
本系统采用YOLOv5作为主要目标检测算法,其原因如下:
实时性强:YOLOv5采用单阶段检测架构,速度快,适用于工业自动化生产线。
鲁棒性高:能够适应不同光照条件和复杂背景,减少误识别率。
训练与部署灵活:支持边缘计算设备(如Jetson Xavier NX),可在本地处理,提高系统稳定性。
6.2 目标定位与姿态估计
在机器视觉定位任务中,不仅要识别目标物体,还需要准确估算其位置信息和旋转角度。
亚像素级角点检测:使用Harris角点检测和亚像素级优化方法,提高边缘检测精度。
PnP算法(Perspective-n-Point):结合摄像机的内外参数,通过多个特征点计算目标的空间位姿信息,适用于三维定位任务。
ICP(Iterative Closest Point):用于点云匹配,适用于高精度三维定位,如机械臂抓取应用。
6.3 视觉引导路径规划
在机器人引导场景中,路径规划是关键步骤。采用以下算法提高路径精度:
A 算法*:适用于静态环境的最短路径搜索,如AGV小车的轨迹规划。
D 算法*:适用于动态环境,能够动态调整路径,适用于无人搬运车的自主导航。
RRT(快速探索随机树):适用于复杂环境的路径规划,如机械臂避障运动规划。
结合上述算法,系统可以在不同应用场景下提供最优的路径引导方案,提高自动化作业的效率。
7. 光学系统设计与优化
在机器视觉系统中,光学系统的设计直接影响图像质量,进而影响定位精度。
7.1 镜头选择
本系统采用Computar M1614-MP2工业镜头,主要考虑以下因素:
高分辨率:支持高达1600万像素的成像,确保采集到清晰的目标图像。
低畸变:减少图像畸变,提高测量精度,适用于精密工业检测。
大光圈设计:在低光环境下依然能获得足够的曝光,提高检测可靠性。
7.2 光源选择
机器视觉系统常用光源包括LED光源、激光光源和红外光源。针对不同应用,选择适当的照明方式能提高检测稳定性。
环形光源:用于均匀照明,如表面缺陷检测。
同轴光源:用于反光表面检测,如金属零件检测。
背光源:用于轮廓检测,提高边缘识别精度。
本系统采用CCS LFX3-100SW 白光LED面光源,确保均匀照明,减少阴影干扰,提高识别准确率。
7.3 滤光片与光学调节
为了提升目标识别的对比度,使用Midwest Optical BP660 滤光片,能够滤除不必要的环境光,提高检测效果。同时,采用自动曝光调节和自适应白平衡算法,提高不同光照条件下的稳定性。
8. 通讯与数据传输设计
机器视觉系统的数据处理量大,需要高效的通讯方式以确保实时性。
8.1 相机数据传输
本系统采用GigE Vision 协议,通过千兆以太网进行数据传输,优点包括:
远距离传输:相比USB接口,支持长达100米的传输距离,适用于工业环境。
高带宽:千兆以太网带宽高达1Gbps,能够实时传输高清图像。
稳定性强:比USB接口抗干扰能力更强,减少信号丢失的风险。
8.2 控制信号传输
采用Modbus TCP协议用于上位机与控制器的通讯,支持多设备联网,易于集成到SCADA系统,实现远程监控与管理。
8.3 物联网(IoT)集成
系统支持MQTT协议,可将视觉数据上传至云端,实现远程分析与优化。结合5G模块(如Quectel RM500Q),能够在大规模生产线中实现高速无线数据传输。
9. 误差补偿与系统校准
9.1 镜头畸变校正
由于工业相机镜头会引入一定的畸变,使用张正友标定法进行镜头校正,以消除畸变影响,提高测量精度。
9.2 视觉误差补偿
在实际工业应用中,由于光照、环境温度等因素,系统可能存在误差。本方案采用神经网络误差补偿模型,通过深度学习不断优化定位精度。
9.3 机械偏差补偿
结合高精度激光测距传感器(如Keyence LK-G5000系列),能够实时调整机械误差,提高定位精度。
10. 可靠性测试与环境适应性
10.1 振动与冲击测试
在工业生产环境中,设备可能面临振动与冲击。本系统采用工业级加固外壳,并通过MIL-STD-810G 冲击测试,确保设备在恶劣环境下依然稳定工作。
10.2 温湿度适应性
系统的电子元件经过高低温循环测试(-40°C 至 85°C),适用于各种极端环境。此外,采用防水防尘设计(IP67 级),确保设备在恶劣工业环境下稳定运行。
11. 机械结构与安装方式
11.1 视觉系统安装方式
机器视觉定位与引导系统的安装方式对其稳定性和测量精度有重要影响。常见的安装方式包括:
固定式安装:适用于流水线检测,工业相机和光源安装在固定支架上,确保拍摄角度一致,提高识别精度。
机械臂集成式安装:用于机器人引导,视觉系统安装在机械臂末端,可灵活调整视角,适应不同工件。
移动式安装:如无人搬运车(AGV)上的视觉导航,需考虑减震措施以降低振动影响。
本系统采用高精度铝合金支架,结合防震减震结构,减少机械振动对成像质量的影响。
11.2 机械误差补偿
为了提高视觉定位精度,系统需考虑机械误差的影响。主要误差来源包括:
安装倾斜误差:由于安装不够精准,摄像头可能存在倾斜,需要在软件层面进行透视校正。
热胀冷缩误差:设备在高低温环境中可能发生微小形变,采用高精度光学尺进行实时补偿。
机械抖动误差:通过陀螺仪(如MPU9250)和加速度传感器实时检测运动状态,动态补偿视觉误差。
12. 软件架构与接口设计
12.1 软件架构
本系统的软件架构采用模块化设计,包括以下核心部分:
图像采集模块:控制工业相机采集图像,并进行预处理(去噪、白平衡)。
图像处理模块:执行目标检测、特征点提取和位姿计算等任务。
通讯模块:与PLC、机器人控制器进行数据交互,支持Modbus TCP和EtherCAT协议。
用户界面(GUI)模块:提供友好的交互界面,支持实时图像显示和参数调整。
12.2 软件开发环境
操作系统:基于Ubuntu 20.04 + ROS 2,提供实时任务调度和多传感器融合能力。
编程语言:采用Python + C++,Python用于算法开发,C++用于底层驱动和高效计算。
深度学习框架:使用PyTorch训练模型,并利用TensorRT优化模型推理速度。
12.3 API接口
系统提供标准化API,支持外部设备集成,主要接口包括:
图像采集接口:提供图像数据流,支持实时处理。
目标识别接口:返回目标类别、位置和置信度信息。
机器人控制接口:支持位置调整、抓取控制等功能。
13. 实时性优化
13.1 硬件加速
为了提高视觉系统的实时性,采用并行计算和硬件加速技术,包括:
GPU加速:使用NVIDIA Jetson AGX Orin进行深度学习推理,加速目标检测算法。
FPGA加速:采用Xilinx Zynq UltraScale+ MPSoC加速边缘计算任务,如特征提取和匹配。
多线程处理:在软件层面,采用多线程优化,提高图像处理和数据传输的并行度。
13.2 低延迟数据传输
系统采用低延迟传输协议,包括:
14. 远程监控与维护
14.1 远程监控
系统支持远程监控,采用Web界面+云端服务器架构,具备以下功能:
14.2 远程维护
15. 安全性设计
15.1 数据安全
15.2 硬件安全
本系统结合高精度光学设计、深度学习优化、实时硬件加速、远程维护等先进技术,提供了一套高效、可靠的机器视觉定位与引导方案。
1、本文内容、数据、图表等来源于网络引用或其他公开资料,版权归属原作者、原发表出处。若版权所有方对本文的引用持有异议,请联系拍明芯城(marketing@iczoom.com),本方将及时处理。
2、本文的引用仅供读者交流学习使用,不涉及商业目的。
3、本文内容仅代表作者观点,拍明芯城不对内容的准确性、可靠性或完整性提供明示或暗示的保证。读者阅读本文后做出的决定或行为,是基于自主意愿和独立判断做出的,请读者明确相关结果。
4、如需转载本方拥有版权的文章,请联系拍明芯城(marketing@iczoom.com)注明“转载原因”。未经允许私自转载拍明芯城将保留追究其法律责任的权利。
拍明芯城拥有对此声明的最终解释权。